Home > Capabilities > Fabricate
Fabricate
At ALMAG, we use numerous types of multi-purpose fabrication equipment for many of the standard processes performed on aluminum parts. This allows us to provide our customers with complete solutions that fit their needs. We have in-house fabrication capabilities as well as trusted partners to ensure any manufacturing challenge can be met with the right process and in the shortest possible lead time.
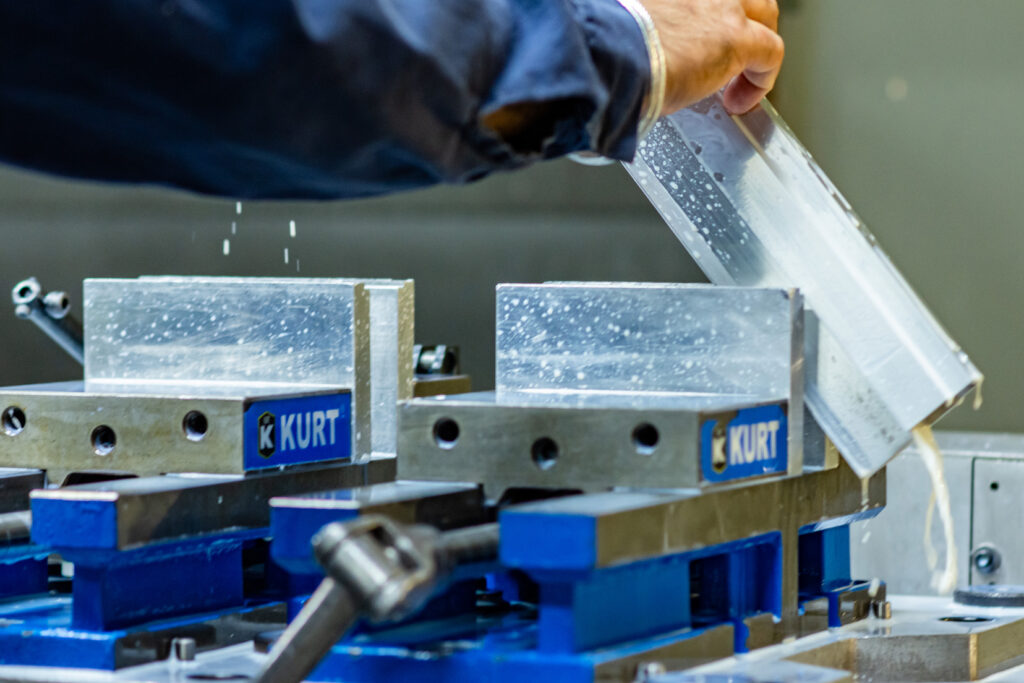
Fabricating capabilities
ALMAG uses precision cutting saws on extrusions to perform cutback operations, which are later deburred. Our equipment includes brake presses to perform punching, notching and closing operations to create customer-specific features. We have drilling and tapping machines for features used to integrate and fasten features with other components.
- Cutting
- Countersinking
- Punching
- Notching
- Bending
- Deburring
- Drilling
- Tapping
- Milling
- Forming
- Mitre Cutting
- CNC machining
Fabricate
CNC capabilities
For precision machining operations, we have multiple CNC machines with a variety of capabilities.
Whether your requirements are for small components or parts that are up to 24 feet in length, we have the ability to meet a wide range of CNC operations. We have capabilities to provide 3 axis, 4 axis and 5 axis machining, both internally and along with a network of trusted partners.
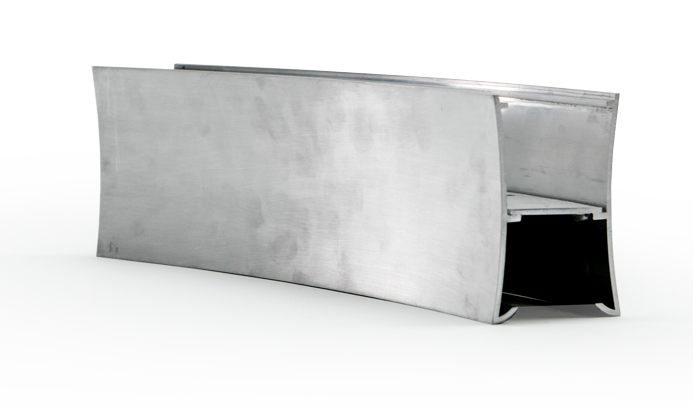
Case Study
Bent Light Fixture
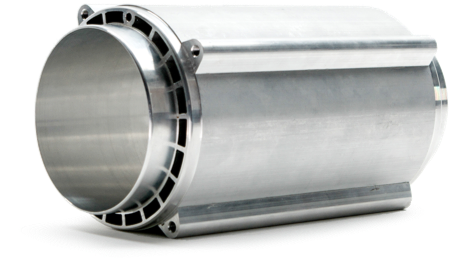
Case Study
Electric Motor Housing
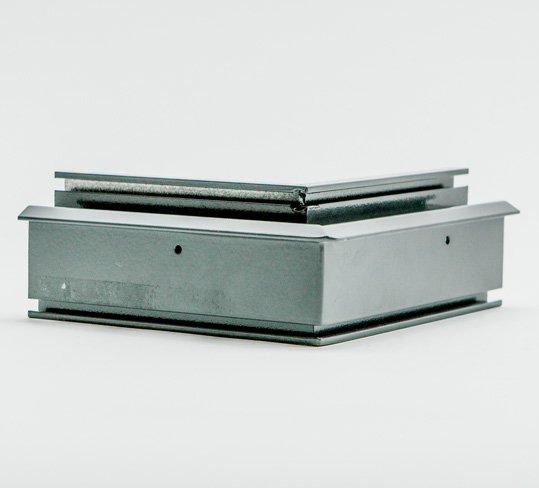
Case Study
Outdoor Retail Display Frame
Eager to find new challenges, we look forward to partnering with you so your next design can be made possible!
We understand that sometimes it takes a little inspiration to get started and see what’s possible. ALMAG’s Inspire tool shows a number of design elements, as well as fabrication and finishing processes, that can be used in a variety of applications. Explore the possibilities and inspire your next design.